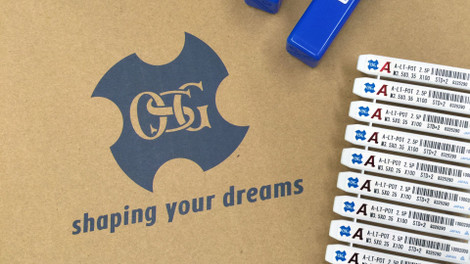
Important Notice Regarding Counterfeit Products
24th Jun 2025
Thank you for your continued patronage of OSG products. It has come to our attention that, in recent years, counterfeit products bearing unauthorized imitations of our corporate logo have entered circ…